Articles
19/08/24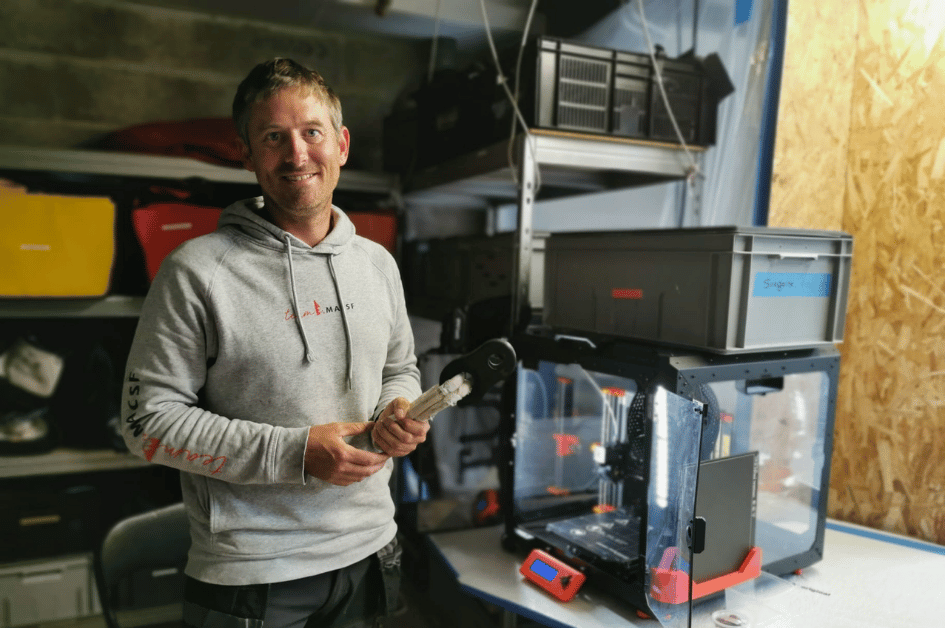
Depuis l’hiver 2023, le team technique Voile MACSF s’est doté d’un nouvel allié : une imprimante 3D. Cette petite machine présente de nombreux avantages : gain de temps, réduction des coûts et des déchets, fabrication sur-mesure… Mais à quoi sert-elle précisément ?
Évidemment, l’objectif ici n’est pas de remplacer le travail des fournisseurs, mais de gagner du temps. - Florian Giffrain, boat captain
Le team a régulièrement recours à l’impression 3D pour produire des moules, de formes diverses. Réutilisables, ces derniers permettent de réaliser des pièces sur-mesure pour l'IMOCA MACSF. Par exemple, de petites équerres ont récemment été produites en suivant ce processus. Fixées sur le bateau, elles servent de supports aux boîtiers électroniques, avec un coût de revient avoisinant les 25 centimes d’euros.
Autre avantage non négligeable : le gain de temps. Certains éléments d’accastillage nécessitent une période d’usinage relativement longue. Avant de lancer leur production, il est donc impératif de s’assurer que la pièce à fabriquer soit bien conforme au cahier des charges. C’est là que l’impression 3D joue un autre rôle intéressant, en étant capable de produire rapidement des pièces en plastique à l’échelle 1, avant de les envoyer en production dans leur matériau final.
Florian Giffrain, boat captain explique : « Prenons l’exemple de notre nouvelle cadène de J2. La fabrication de cette pièce en titane coûte très cher. Pour être certains de ne pas nous tromper dans la commande, nous avons conçu un échantillon avec l’imprimante 3D. Évidemment, l’objectif ici n’est pas de remplacer le travail des fournisseurs, mais de gagner du temps. Sept heures d’impression suffisent pour créer le gabarit de la cadène de J2 ».
Fort d’un BTS de concepteur industriel, Florian maîtrise la CAO (Conception Assistée par Ordinateur) et le DAO (Dessin Assisté par Ordinateur). C’est donc naturellement qu’il a proposé à l’équipe de se doter d’une imprimante 3D, et d’en assurer la gestion.
Chaque projet démarre par un croquis sur papier et la rédaction d’un cahier des charges (dimensions souhaitées, analyse des forces et charges en présence, choix des matériaux...). Vient ensuite le temps du dessin de la pièce sur ordinateur, avec un logiciel 3D (par exemple Fusion 360, SolidWorks, Rhinoceros 3D, AutoCAD 3D…). Le logiciel permet d’identifier les points sensibles de la pièce (rouge = risque de casse), invitant à redessiner la pièce jusqu’à obtenir une structure homogène, dénuée de risques de rupture. Une fois le projet finalisé, on l’envoie sur le logiciel de l’imprimante (à titre indicatif, la taille du plateau de l’imprimante de l’équipe mesure environ 25 cm2, avec la possibilité d’imprimer en hauteur et d’assembler les pièces entre elles). On indique alors le taux de remplissage souhaité (pièce creuse ou pleine) ainsi que le prix d’achat de la bobine de matière à imprimer (plastique, carbone, céramique…) afin de calculer le coût de revient final de la pièce qui sera produite. Une fois la pièce imprimée, on la soumet à une série de tests en configuration réelle. Si ces derniers sont concluants, il ne reste plus qu’à envoyer le plan chez l’usineur.
Articles en relation
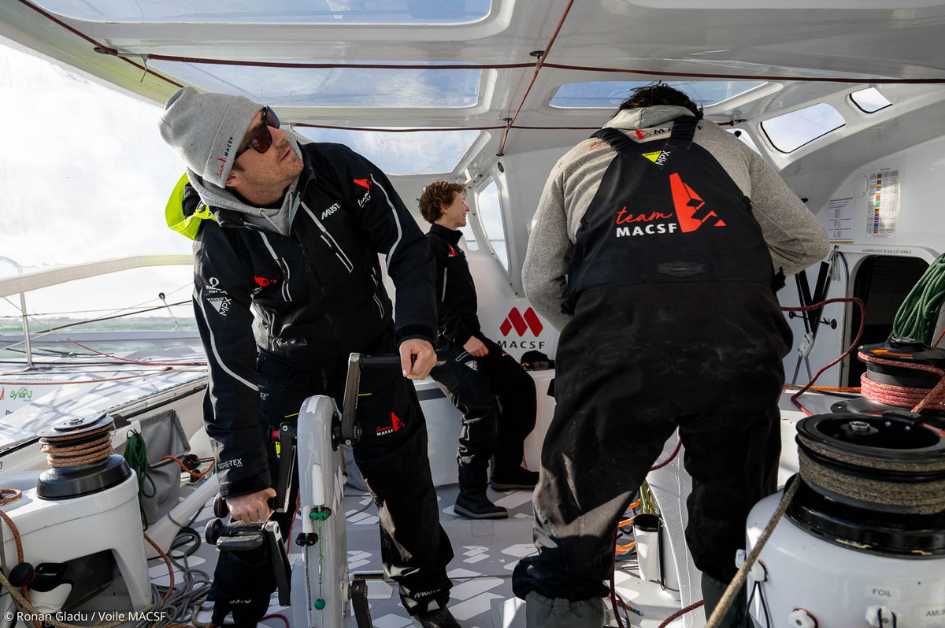
En amont du traditionnel chantier d’été, qui sera lancé à partir du 8 juillet, une série d’entraînements, au large de Lorient, permet au team technique et à Isabelle Joschke, skipper MACSF, de basculer définitivement l’IMOCA en mode « Vendée Globe ». Aspects sportifs, techniques, sécurité : aucun détail n’est laissé au hasard et tout est mis en œuvre pour se projeter le plus sereinement possible.
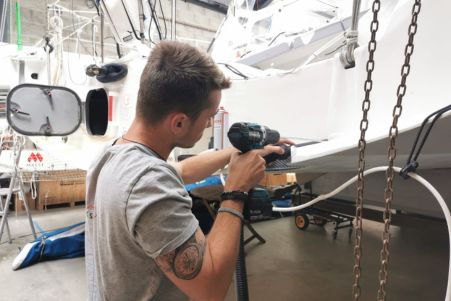
Depuis le 8 juillet, date de sa sortie de l’eau, l'IMOCA MACSF a retrouvé son hangar pour entamer un nouveau chantier d'été. Bien que court, ce chantier permettra au team MACSF d’apporter les dernières améliorations qui permettront de faciliter autant que possible la vie d’Isabelle Joschke, skipper MACSF, à bord pendant le Vendée Globe.
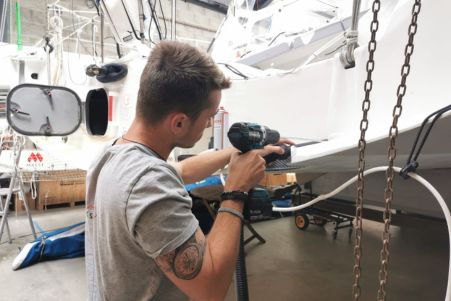
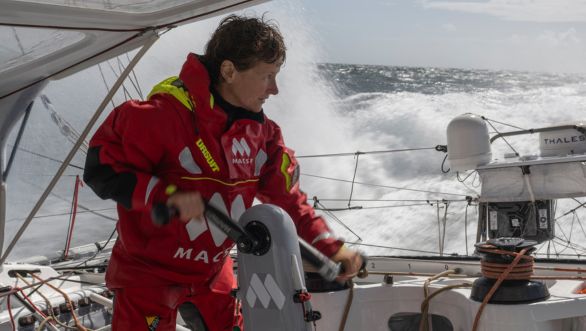